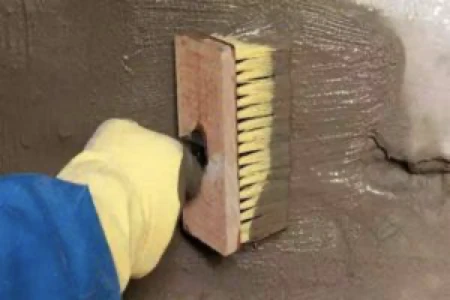
1. Cement Based Waterproofing Material
The construction of cement-based waterproofing is considered a trouble-free waterproofing method. It is very easy to mix and use materials for cement-based waterproofing. This method is often preferred for interior wet areas such as bathrooms and toilets. This system is a two-component mix typically used behind tile, on wall patches, and on concrete surfaces. These top and bottom grade waterproofing materials have good bonding on concrete and masonry surfaces due to their cementitious nature and hence their strong adhesive strength. The polymer modifier contributes to the flexibility properties.
Scope of application:
- Indoor and Outdoor Areas
- Wet Areas
- Retaining Walls
- Water Tanks and Swimming Pools
- Elevator Pits
- Metro Stations
- Tunnels
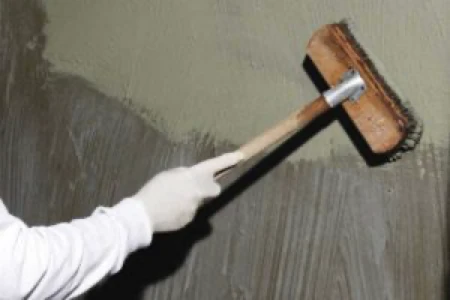
2. Crystallized Waterproofing Material
Crystallized waterproofing is a capillary waterproofing formulation of proprietary chemicals, quartz sand and cement mixtures. The chemicals contained in crystalline waterproofing materials require the presence of moisture from the matrix of concrete to initiate a chemical reaction. These chemicals form chain complexes that crystallize and penetrate deep into the capillaries of the concrete, eliminating the passage of water.
Scope of application:
- Wet Areas
- Water Tanks
- Elevator Spaces
- Subway Tunnels
- Underground Cellars
- Basement Floors
- Retaining and foundation curtain walls
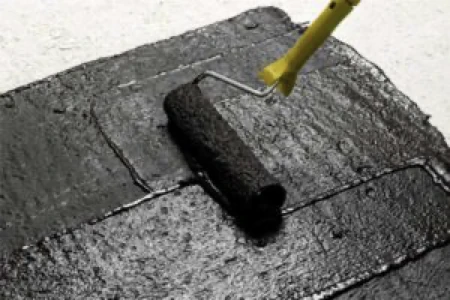
3. Bitumen Rubber Based Waterproofing Material
Liquid rubber bitumen liquid membranes is a polymer-modified bitumen-rubber emulsion. Bitumen-polymer mixture / liquid rubber coating has traditionally been offered on the market as a waterproof waterproofing coating. Recently, the liquid rubber coating has been further developed and can now be used for excellent sealing on a variety of surfaces.
The differences in coatings are mainly in the viscosity and basis of the variant (natural base (latex) or artificial base (silicones)). It is designed to be environmentally friendly and to provide excellent waterproofing for roof structures. The unique properties of the coating are that it is effective, easy to apply and cost effective.
Liquid rubber coating is a widely used product for special purposes. There is no doubt: it is a very reliable sealant and coating agent that can be applied even to damp surfaces. This also makes it a great solution for large or industrial projects.
Scope of application:
- Retaining Walls, Basements and Basement Walls
- Flower Pots, Garden Beds, Landscape Areas
- Water Tanks (galvanized, suitable for metal tanks)
- Gutter, Roof and Membrane Repairs
- Rust Prevention and Timber Rot Protection
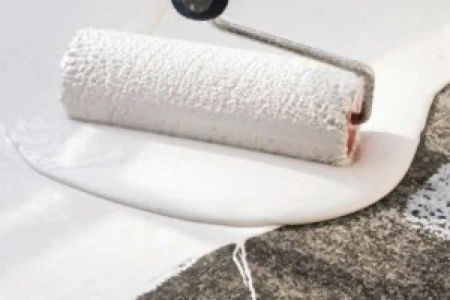
4. Acrylic Liquid Membrane Waterproofing Material
Water-based acrylic waterproofing materials produced with modern technologies are simple and ready to use. They form an effective barrier against water and moisture to protect roofs, terraces and balconies from leaks and the negative effects of UV rays. The waterproofing industries have changed significantly since the industry developed acrylic waterproofing materials. In general, waterproofing companies immediately adopted and implemented these solutions, which simplifies the process and at the same time guarantees accurate and effective waterproofing with no waste of material. It also allowed for unexpectedly easy cleaning of work sites, and most importantly, for safety issues, the transport and use of gas tanks to burn conventional bituminous membrane is no longer necessary.
Acrylic liquid waterproofing membrane is available in liquid form and is applied to the concrete surface with a brush or roller, creating a thick, jointless surface in contact with air. It offers more flexibility than cementitious waterproofing types. The liquid turns into an elastic coating on the wall. The elongation properties of the coating can be up to 300%. The durability of the coating depends on what kind of polymer is used in the manufacture of the liquid waterproofing material.
Scope of application:
- Roofs and Terraces
- Sub-Foundation Structures
- hidden stream
- Metal or concrete gutters
- Curtain concrete
- Basements
- Catwalks
- Bridge Decks
- Wet Areas
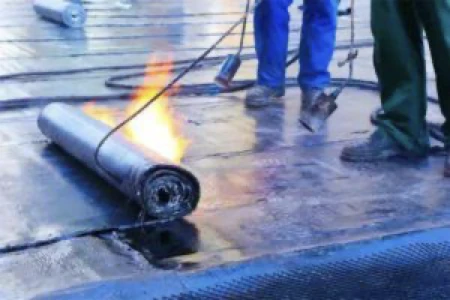
5. Bituminous Membrane Waterproofing
As a long-lasting waterproofing solution, bitumen waterproofing membrane is applied in a dry area using bitumen-based sheets. These are then rolled down to cover the roof or wall while being melted to the surface by a torch. Bituminous membrane is non-toxic, but requires precision and skill, especially in the areas where the joints meet. By spreading the descending layers of the bituminous membrane evenly, a coating surface resistant to adverse weather conditions is gained.
Bituminous Membrane Waterproofing is known for their long service life, reliability and exceptional waterproofing. The two main polymer modified bitumen membranes on the market are SBS and APP membranes.
SBS Membranes are made with bitumen modified with elastic Styrene-Butadiene-Styrene (SBS) polymers to create a “plasticized” asphalt pavement. The coating is applied to a glass fiber reinforcement carrier for high tensile strength, polyester or a composite of the two for superior elongation and tear strength. SBS membranes offer excellent flexibility, especially in cold weather. SBS membranes are self-adhesive but are usually bonded with asphalt or cold glue.
APP Membranes are made with bitumen modified with plastic Atactic Polypropylene (APP) polymers. This results in a coating with the highest temperature range and increased durability and toughness. The coating is usually applied over a polyester carrier mat, but a small amount of fiberglass products are also available. APP membranes are applied with torch mainly because the plasticized bitumen is fusible.
Scope of application:
- Retaining walls, basements and underground structures
- Flat roofs under protective layers
- Underground car parks
- Bridges
- Raft flooring and foundations
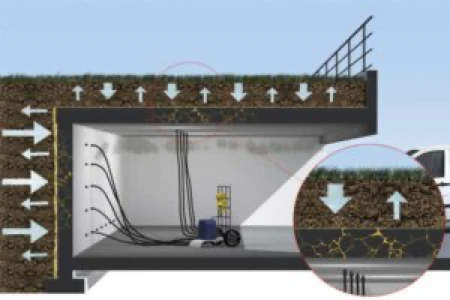
6. Polyurethane-Injection Waterproofing
Injection is a waterproofing technique that uses expanded, injected polyurethane to prevent water from flowing through it, typically using voids or cracks in the concrete. This is particularly effective in solving water leak problems when applied below the leak area or on the subfloor ceiling where the leak is occurring. After the polyurethane injection goes through a water expansion process, any cracks filled will have a mixture of water and polymer foam type polyurethane mortar. The mixture will then expand until there is no room to fill, successfully closing the paths where water enters the material.
A hole will need to be drilled in the lower part of the ceiling first to allow the polyurethane foam to be injected using a pressure machine. The pressure causes the polyurethane to rise into cracks or voids from water damage, which fills completely when it expands. Polyurethane injection is a recommended method to be applied to actively leaking cases involving concrete slabs.
Scope of application:
- Wet areas including toilets, showers and kitchens
- Concrete, tile or metal roofs
- Balconies and terraces
- Basements, foundations and retaining walls
- Water Tanks
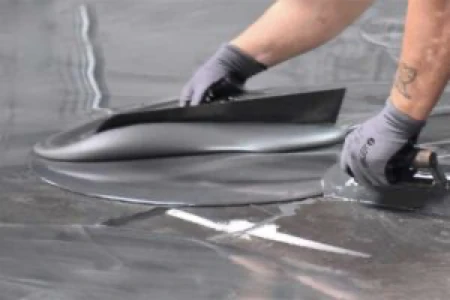
7. Epoxy Floor Coatings
Epoxy floors are water resistant, stain resistant and can withstand contact with corrosive chemicals. This makes the epoxy an excellent choice for high-traffic areas such as residences, bedrooms, bathrooms, garages and basements, commercial showrooms and warehouses. Epoxy floor coatings can be cleaned quickly and easily with a mop and a mild cleaning solution, making it a maintenance-free flooring option.
Epoxy floor coatings also form a very costly seal to repair, which can prevent damage to the underlying concrete. Epoxy floor coatings create a scratch resistant surface that can withstand 7-20+ years of tough use. Also, epoxy is fire resistant, which is one of the reasons it is often used in industrial buildings.
Epoxy floors are free of any joints, wrinkles or pores for dirt and bacteria to get into. As a result, pathogens and other microscopic organisms are less likely to spread in an epoxy-based environment. Because epoxy creates an even surface, there’s no need to remove grout or dirt settling between the seams as with tile, wood, and vinyl floors. This makes it an excellent choice for both commercial and residential use.
The gloss of the epoxy floor creates a high-end surface that can be customized to suit a variety of styles and applications. Epoxy is available in a variety of colors to suit any design requirement. It can also be used to create a marble effect or combine with vinyl flakes for a mottled effect. Because there are so many design possibilities, epoxy is an excellent choice for homeowners and businesses.
Scope of application:
- White Goods Coating Applications
- Steel Corrosion Resistant Coatings
- Metal Box and Container Coating
- Flooring Applications
- Car Park
- Hotels
- Industrial Floors
- Hospitals
- Production Facilities
- Aircraft Hangars
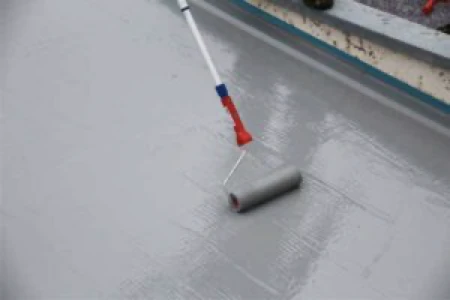
8. Polyurethane Liquid Membrane Waterproofing Material
Polyurethane Liquid Membrane Waterproofing Materials are formulated using monomers such as polyether polyol and isocyanate. This waterproof coating is applied to the horizontal surface to make it moisture resistant. The treated surface tends to react chemically with moisture in the air to produce elastomeric rubber-based waterproof membranes.
The waterproofing system of the polyurethane liquid membrane is used in the flat roof area and has a wide opening against weather conditions. Polyurethane liquid membrane waterproofing system is quite costly compared to another waterproofing system. However, this is the best waterproofing material in the industry. Higher durability can be achieved with the polyurethane liquid membrane. Polyurethane is very sensitive to moisture content. Therefore, the moisture content of the concrete slab should be evaluated very carefully before application. Otherwise, the membranes may peel or loosen after a while.
Scope of application:
- Roofs, Terraces and Balconies
- Water Tanks, Ornamental Pools and Swimming Pools
- Bridges
- Parking Areas
- Concrete Structures
- Decks
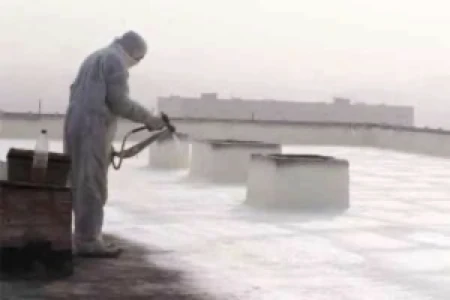
9. Polyurea Spray Coating
Polyurea is the latest advancement in coating technology providing the best in the world. Its extreme durability is 20 times stronger than some epoxy coatings. Polyurea does not crack or peel. It is highly resistant to salt, oil, fuel and other harsh chemicals. It is 98% more flexible than epoxy, allowing natural concrete movement. It has been used for over 25 years in industrial applications such as pipe/pipeline linings, tank linings, water treatment plants, sewer linings and automotive moldings. It cures in 5-15 seconds and must be sprayed for proper installation. Such coatings were originally developed and used in the early 1990s.
Polyurea forms a very strong bond with concrete due to its chemical structure. It has the ability to expand and contract with the change in surface and the temperature of the underlying ground. This means no chips, cracks or hot rubber buildup. Hot tire buildup occurs when a car’s tires are hot from driving; heat and pressure from tires can melt or peel paint or coating, separating it from the floor. However, Polyurea is a “hard” surface that is highly resistant to abrasion. It retains its color and does not fade or turn yellow when exposed to direct sunlight.
Polyurea Coating can be applied at temperatures such as 4 °C ~ 49 °C. This is important because most waterproofing applications are not performed in a climate-controlled environment, providing greater flexibility in deciding when to install the coating. Polyurea cures much faster than other polymer-based coatings. Typically suitable for foot traffic on the ground 4-8 hours after installation and for heavy vehicle traffic 24 hours after installation.
Scope of application:
- Roofs and Terraces
- Landscape Areas
- Pipeline Coatings
- Tank Paints and Coatings
- Floors and Walls
- Structural Steel
- Automotive Molding Parts
- Bridge Covering